In 3D Printing News Briefs, we start with business today, as UpNano has announced its expansion into the United States. Next, we have news on medical 3D printing, aerospace 3D printing, and offshore 3D printing. A team of European researchers has experimented with adding recycled glass to cement composites to print buildings. Finally, a German designer and architect has come up with an odd-looking shoe designed to be 3D printed from flexible TPE using Sintratec’s laser sintering technology.
UpNano expands to the United States
First, UpNano GmbH, a spin-out of TU Wien, a leader in two-photon polymerization (2PP), announced that it will expand its operations in the United States. This decision is due to the solid financial situation of the Austrian company and the strong interest of the American market, as it announces a year in which sales have tripled. The technology company’s NanoOne series of laser-powered 2PP 3D printers are said to be capable of printing high-speed, high-resolution structures over 12 orders of magnitude. As part of the expansion, Erika Bechtold, PhD, currently director of technology commercialization at Harvard’s Office for Technology Development, which supports the Wyss Institute for Biologically Inspired Engineering, will serve as vice president of US operations. in Boston, Massachusetts. Dr. Bechtold has over ten years of business development and business strategy experience that she brings to this role.
“I am so impressed with the NanoOne systems the team has built. UpNano is at a pivotal time in its growth and I am excited to join the team to help promote this commercial-stage system in the United States. is such a great opportunity at a time of notable growth in the 2PP 3D printing markets,” said Dr. Bechtold.
Extol Obtains FDA Registration for Contract Manufacturing of 3D Printed Medical Devices
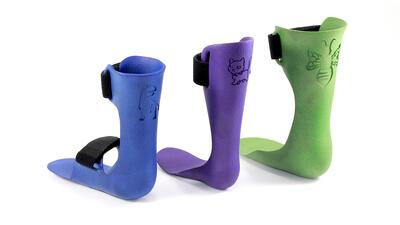
Spentys orthoses manufactured by Extol
Digital manufacturing technology company Extol, Inc. announced that it has received FDA registration for turnkey contract manufacturing of 3D printed medical devices. This new FDA registration will allow Extol to expand its 3D printing offerings for the life sciences industry. The company will likely see an immediate positive impact in its ability to offer complete 3D printed solutions for medical devices in the orthotics and prosthetics (O&P) market. In addition to 3D printing, Extol will also offer post-processing, final assembly and order fulfillment of finished medical devices.
As Kyle Harvey, director of Extol’s business unit for additive manufacturing, explained, “Digital manufacturing with 3D printing is disrupting the way people make products in almost every industry.
“Digital transformation is well advanced in the O&P industry to create better outcomes for patients using medical devices. We are very happy to support O&P partners and practitioners investing in digital workflows. »
Aurora Labs Campaign to Demonstrate Metal 3D Printing for Aerospace Standards

Gland trackers 3D printed using 4-laser 1.5kW parameter sets on the RMP-1 Beta
Australian industrial technology company Aurora Labs has announced a new printing demonstration campaign, in which the metal 3D printer it is developing will run for 1,000 hours in less than three months. This will demonstrate that the company’s prototype printer, subsystems and beta architecture can meet the rigorous standards of the SAE AMS7039 and AMS7032 International Aerospace Printing Specification Projects. The project is approved by The Barnes Global Advisors, who offered analysis and consultation during the marketing phase. The four-phase project, consisting of 24 releases, will print parts in 316L stainless steel, which will then undergo a variety of metallurgical, mechanical, X-ray and chemical tests. The results of the more than 500 test specimens must be consistent and reproducible over the four phases.
“We look forward to completing the demonstration campaign and sharing the results with potential customers, partners and the wider AM community. A successful result will validate our capability for a wide range of industrial applications that Aurora is pursuing, and not just limited to aerospace,” said Peter Snowsill, CEO of Aurora Labs. “Methodically demonstrating A3D’s technology with careful data collection is an important part of our go-to-market strategy, adding to a bank of information that can be shared with potential partners. The results will also help in finding contract printing customers as we promote printing services to local industry. We are confident of success and look forward to presenting the results.
Woodside activates a 3D printed valve on an offshore platform
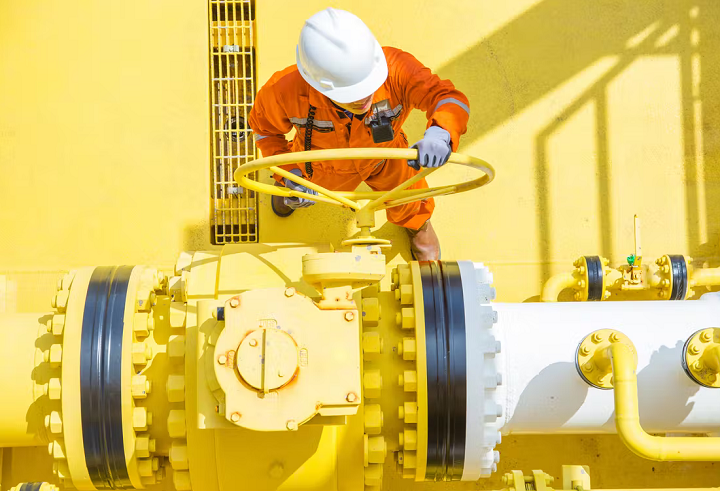
Overseas staff
Another Australian company, Woodside Energy, has installed and activated a 3D-printed valve on its Goodwyn A offshore platform, part of its North West Shelf (NWS) project. Monash University’s FutureLab helped redesign a stainless steel monoflange body for 3D printing, which has been approved for use in critical service under pressure. The part is a dual shut-off and bleed valve used to safely isolate instruments during maintenance work, and Woodside said the improved design increases flow by not restricting channel junctions. The company will then focus on a 3D-printed steel inductor on the Okha FPSO platform at the NWS complex.
“It can be energy-intensive, time-consuming and expensive to find replacement parts for such parts,” said Shaun Gregory, executive vice president for sustainability at Woodside Energy, of how 3D printing can help solve problems when it comes to replacing parts that OEMs can no longer replace. to supply.
Researchers 3D Printing Cscholar Composites with recycled glass

Printing process of specimens (a) and (b) and determination of flexural strength (c).
A team of researchers from the Technical University of Berlin and Brunel University London recently published an article about their work using recycled glass as a component of concrete for 3D printing buildings. Their hope is to reduce the significant environmental impact of concrete, as the construction industry creates around 35% of all waste in landfills worldwide. Concrete is made up of water, cement and aggregates like sand. So the team replaced up to 100% of the aggregates in their mix with glass, which is easy to recycle and is actually produced from sand. They crushed soda-lime glass bottles from a local recycling company, then washed, dried, crushed and sieved the pieces to make concrete. The team succeeded in 3D printing wall elements and prefabricated building blocks from their cementitious composite material. They also took care to make their material more durable: the type of glass they used has increased thermal conductivity; they replaced some of the Portland cement with less dangerous limestone powder; and they added light fillers to reduce the density of the concrete.
“The presence of glass not only solves the problem of waste but also contributes to the development of a concrete with superior properties to that containing natural sand. Used in this way, glass waste can find a new life as a building material,” write Seyed Ghaffar Medhi Chougan and Pawel Sikora, two of the co-authors.
“Our research shows that an ultra-lightweight, well-insulated 3D building is possible – something that could be a vital step in our mission to net zero.”
Unique 3D Printed Shoes Make Bigfoot Tracks
Finally, I bet you’ve never seen anything quite like the Cryptide sneaker – fully 3D printed shoes with soles that make tracks like Bigfoot would! German designer and architect Stephan Henrich created the shoe, which is obviously inspired by mythical Cryptid creatures, such as the Loch Ness Monster or Bigfoot. Composed of an open design sole and combined with a thin upper shoe, they were laser sintered on the Sintratec S2 printer from its flexible and rubbery TPE elastomer. Although it may seem odd, the Cryptide shoe is more ergonomic and comfortable to wear, as Henrich varied the wall thickness to make some parts soft and flexible and others stiff.
Henrich confirmed: “If you wear this shoe, you will leave traces like a cryptid would.”
Subscribe to our newsletter
Stay up to date on all the latest 3D printing industry news and receive information and offers from third-party vendors.